Calibração de manômetros como garantir precisão e eficiência
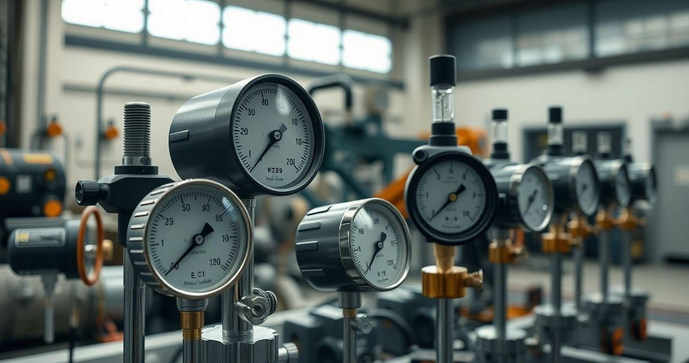
Por: Thiago - 17 de Abril de 2025
Importância da calibração de manômetros na indústria
A calibração de manômetros é fundamental na indústria, pois assegura medições precisas de pressão, essenciais para a eficiência operacional. Quando os manômetros estão devidamente calibrados, as medições são confiáveis, permitindo que os equipamentos operem dentro dos parâmetros desejados, evitando falhas e acidentes. Além disso, a calibração ajuda a manter a conformidade com normas e regulamentações, que muitas vezes exigem que os instrumentos de medição sejam verificados regularmente. Isso não só garante a segurança dos trabalhadores, mas também previne perdas financeiras devido a erros de medição. Uma medição imprecisa pode levar a decisões inadequadas, como a utilização excessiva de recursos e a incapacidade de identificar falhas em sistemas, resultando em danos significativos. Em resumo, a calibração de manômetros é um aspecto crítico da manutenção de equipamentos industriais, contribuindo para um ambiente de trabalho seguro e produtivo.
Principais métodos de calibração de manômetros
Existem vários métodos para a calibração de manômetros, cada um com suas particularidades e aplicabilidades. Os principais métodos incluem:
1. Calibração por comparação: Neste método, o manômetro a ser calibrado é comparado com um instrumentação de referência de alta precisão. Em um ambiente controlado, as medições são realizadas simultaneamente para verificar possíveis desvios e ajustar o manômetro conforme necessário.
2. Calibração com o uso de padrões de pressão: Este método utiliza padrões de pressão, como bombas pneumáticas ou hidrostáticas, para gerar pressões conhecidas. O manômetro é exposto a essas pressões, e as leituras são registradas para análise.
3. Calibração eletrônica: Com o avanço da tecnologia, a calibração eletrônica tem se tornado comum. Equipamentos especializados emitidos por dispositivos digitais fornecem medições precisas e facilmente registráveis, permitindo ajustes automáticos e rastreabilidade de dados.
4. Calibração em campo: Para manômetros instalados em locais de difícil acesso, a calibração em campo pode ser a melhor solução. Utilizando um manômetro de referência portátil, é possível realizar a calibração sem a necessidade de desinstalar o equipamento.
5. Calibração por software: Algumas soluções modernas permitem a calibração de manômetros por meio de software, onde os dados de leitura são analisados e calibrados por algoritmos, proporcionando mais eficiência e precisão nos ajustes.
Em cada um desses métodos, é essencial seguir os procedimentos recomendados pelos fabricantes para garantir a precisão e a confiabilidade das medições, contribuindo para a segurança e eficiência das operações industriais.
Equipamentos necessários para calibração eficaz
Para realizar uma calibração eficaz de manômetros, é necessário ter em mãos alguns equipamentos e ferramentas essenciais. A seguir, listamos os principais itens que devem ser utilizados no processo de calibração:
1. Padrões de pressão: Esses instrumentos, como bombas pneumáticas ou hidrostáticas, são fundamentais para gerar pressões conhecidas. Eles servem como referência para comparação durante o processo de calibração.
2. Manômetro de referência: Este é um instrumento de medição de alta precisão, que deve ser calibrado e rastreável a padrões nacionais e internacionais. Ele é usado para comparar as leituras do manômetro que está sendo calibrado.
3. Fonte de alimentação: Para manômetros eletrônicos, uma fonte de alimentação confiável é crucial. Isso garante que o manômetro opere corretamente durante a calibração, sem interferências.
4. Conectores e mangueiras: Mangueiras adequadas e conectores compatíveis são necessários para conectar o manômetro a ser calibrado aos padrões de pressão. Materiais de qualidade garantem que não haja vazamentos que possam comprometer as medições.
5. Multímetro: Um multímetro pode ser utilizado para verificar a corrente e a tensão em manômetros eletrônicos, assegurando que estão operando dentro das especificações corretas.
6. Software de calibração: Muitos sistemas modernos de calibração utilizam software para registrar e analisar dados de medição. Um software apropriado pode automatizar o processo e fornecer relatórios detalhados sobre o desempenho do manômetro.
7. Instrumentos de medição de temperatura: Em alguns casos, a temperatura pode afetar a precisão das medições. Instrumentos confiáveis devem ser utilizados para monitorar e ajustar as condições ambientais durante a calibração.
Dispor de todos esses equipamentos e seguir as práticas recomendadas assegura que a calibração dos manômetros seja realizada com precisão e eficácia, contribuindo para a segurança e eficiência das operações industriais.
Frequência recomendada para calibrações de manômetros
A frequência recomendada para a calibração de manômetros pode variar dependendo de vários fatores, incluindo o tipo de manômetro, o ambiente em que está sendo usado e a criticidade da aplicação. Abaixo, apresentamos algumas diretrizes gerais que podem ser seguidas:
1. Recomendações do fabricante: A primeira fonte de orientação deve ser sempre o manual do fabricante, que geralmente inclui um cronograma de calibração baseado em testes realizados e especificações do equipamento. Seguir essas diretrizes é essencial para manter a validade da garantia e assegurar o funcionamento adequado.
2. Ambientes industriais: Em ambientes industriais com condições extremas, como altas temperaturas ou pressões variáveis, recomenda-se realizar a calibração com mais frequência, geralmente a cada 6 meses. Nestes casos, a pressão constante é essencial para a segurança e eficiência dos processos.
3. Aplicações críticas: Para manômetros utilizados em aplicações críticas, como indústrias de petróleo e gás, farmacêuticas ou alimentícias, a calibração deve ser feita anualmente ou até mesmo semestralmente. Essas indústrias têm padrões rigorosos de segurança e qualidade que necessitam de medições precisas e confiáveis.
4. Uso regular: Para manômetros que são utilizados regularmente, uma calibração anual pode ser suficiente, mas deve-se manter um registro da precisão das medições. Caso sejam observadas discrepâncias frequentes, a frequência deve ser ajustada.
5. Mudanças no processo: Se houver mudanças nos processos, como a introdução de novos materiais ou equipamentos, recomenda-se recalibrar os manômetros para garantir que as medições permaneçam precisas.
6. Testes periódicos: Além da calibração regular, é importante realizar testes periódicos, como verificações de funcionamento e desempenho, para detectar possíveis degradações antes da calibração regular agendada.
Seguir essas diretrizes ajuda a manter a eficácia dos manômetros e assegura que os processos industriais sejam conduzidos com segurança e confiabilidade.
Erros comuns na calibração e como evitá-los
A calibração de manômetros é um processo crítico, mas pode ser suscetível a erros que comprometem a precisão das medições. Conhecer esses erros comuns e como evitá-los é fundamental para garantir a eficácia da calibração. A seguir, listamos alguns dos principais erros e suas soluções:
1. Falta de equipamentos adequados: Um erro frequente é não utilizar padrões de pressão calibrados e certificados. Para evitar isso, certifique-se de que todos os equipamentos de referência estão em conformidade com os padrões nacionais e internacionais de medição.
2. Condições ambientais inadequadas: A calibração realizada em ambientes com temperaturas ou pressões inadequadas pode gerar resultados imprecisos. Realize a calibração em um ambiente controlado, onde temperatura e umidade sejam mantidas dentro dos limites especificados pelo fabricante.
3. Descuido com alinhamentos: Um manômetro mal alinhado pode causar medições erradas. Sempre verifique se o manômetro está posicionado corretamente antes de iniciar o processo de calibração, garantindo que não haja obstruções e que esteja nivelado.
4. Calibração sem planejamento: Realizar calibrações sem um plano estruturado pode resultar em medições inconsistentes. Crie um cronograma de calibração regular, conforme recomendado pelo fabricante e pela criticidade da aplicação, para assegurar que todos os manômetros sejam calibrados de maneira sistemática.
5. Não registrar dados de calibração: Ignorar o registro dos dados de calibração pode levar à falta de rastreabilidade. Mantenha um registro detalhado de todas as calibrações, incluindo datas, resultados e ajustes realizados. Isso facilitará a verificação da precisão ao longo do tempo.
6. Negligenciar manutenção regular: Esperar até a próxima calibração para verificar o funcionamento dos manômetros pode ser um erro custoso. Realize manutenção e inspeções regulares para garantir que o equipamento esteja sempre em boas condições antes da calibração.
7. Uso de métodos incorretos: Utilizar um método de calibração inadequado para o tipo de manômetro pode levar a medições imprecisas. Conheça os métodos de calibração apropriados para cada tipo de manômetro e aplique-os corretamente, de acordo com as especificações do fabricante.
Ao estar ciente desses erros comuns e implementar as soluções adequadas, é possível otimizar o processo de calibração e garantir medições precisas e confiáveis, contribuindo para a segurança e eficiência das operações industriais.
Normas e regulamentos relacionados à calibração de manômetros
As normas e regulamentos relacionados à calibração de manômetros são fundamentais para garantir a precisão das medições e a segurança nas operações industriais. Essas diretrizes estabelecem parâmetros a serem seguidos, promovendo a qualidade e a conformidade com padrões reconhecidos. A seguir, apresentamos algumas das principais normas e regulamentos:
1. ISO 9001: Essa norma estabelece critérios para um sistema de gestão da qualidade e é fundamental para empresas que buscam garantir a qualidade de seus processos, incluindo a calibração de equipamentos, como manômetros. A implementação faz com que as organizações desenvolvam processos eficazes de calibração e verificação da precisão.
2. ISO/IEC 17025: Essa norma especifica os requisitos gerais para a competência de laboratórios de ensaio e calibração. Ela é crucial para garantir que os laboratórios que realizam calibrações operem de acordo com padrões rigorosos, assegurando resultados confiáveis e rastreáveis.
3. NIST (Instituto Nacional de Padrões e Tecnologia): Nos Estados Unidos, o NIST fornece orientações sobre interpretação de medições e calibração de instrumentos. Organizações frequentemente seguem seus padrões para garantir a confiabilidade das medições em diversos setores, incluindo a calibração de manômetros.
4. ANVISA: No Brasil, a Agência Nacional de Vigilância Sanitária estabelece normas para equipamentos que operam em setores regulados, como os de saúde e alimentos. Os manômetros utilizados em processos nesses setores devem seguir as normas da ANVISA, incluindo a calibração regular para garantir a segurança e a eficácia.
5. Diretivas de segurança do trabalho: Normas como a NR 13 (que trata da segurança em caldeiras e vasos de pressão) requerem que manômetros sejam calibrados regularmente para garantir a segurança e a eficiência operacional. O não cumprimento dessas normas pode levar a sanções legais e riscos à segurança dos colaboradores.
6. HACCP (Hazard Analysis Critical Control Point): Esta abordagem preventiva é utilizada na indústria alimentícia e exige que os instrumentos de medição, incluindo manômetros, sejam calibrados regularmente para prevenir riscos à saúde pública.
A conformidade com essas normas e regulamentos assegura que as calibrações de manômetros sejam realizadas de maneira adequada, minimizando os riscos associados a medições imprecisas e garantindo a manutenção da qualidade e segurança em todos os processos industriais.
A calibração de manômetros é essencial para garantir medições precisas e confiáveis, desempenhando um papel crucial na eficiência e segurança das operações industriais.
Ao seguir as melhores práticas de calibração, conhecer os métodos disponíveis, utilizar os equipamentos adequados e respeitar as normas e regulamentos, as empresas podem evitar erros comuns e assegurar a conformidade com padrões reconhecidos.
O investimento contínuo em calibração não apenas previne falhas e acidentes, mas também contribui para a qualidade e a segurança dos processos, promovendo um ambiente de trabalho mais seguro e produtivo.