Calibração de Válvulas de Segurança: Guia Completo para Profissionais
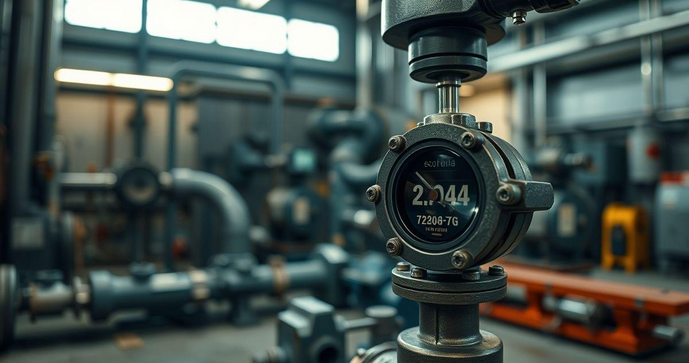
Por: Thiago - 24 de Maio de 2025
Importância da Calibração de Válvulas de Segurança
A calibração de válvulas de segurança desempenha um papel crucial na proteção de sistemas industriais. Essas válvulas são projetadas para liberar pressão excessiva, prevenindo acidentes e mantendo a integridade do equipamento.
Sem uma calibração adequada, as válvulas podem não abrir nas pressões corretas, resultando em falhas catastróficas, como explosões ou vazamentos. Assim, a calibração garante que o sistema funcione dentro dos parâmetros seguros estabelecidos.
Além de prevenir acidentes, a calibração regular das válvulas de segurança é um requisito normativo em muitas indústrias. Agregar essa prática ao seu processo não apenas cumpre as regulamentações, mas também melhora a eficiência operacional e a confiabilidade do sistema.
A manutenção adequada das válvulas de segurança pode levar a reduções nos custos operacionais. Quando calibradas corretamente, as válvulas funcionam de maneira mais eficiente, consumindo menos energia e prolongando a vida útil do equipamento.
Por fim, a calibração não deve ser vista apenas como uma obrigação, mas sim como um investimento em segurança e eficiência. Através de uma rotina de calibração bem estruturada, as empresas podem não só proteger seus funcionários e ativos, mas também garantir a continuidade das operações.
Passo a Passo da Calibração de Válvulas
Para realizar a calibração de válvulas de segurança de forma eficaz, siga um processo estruturado que garanta precisão e segurança.
1. Preparação: Antes de iniciar a calibração, assegure-se de que o ambiente de trabalho esteja seguro e que você tenha todos os equipamentos necessários, incluindo manômetros, chaves de fenda e equipamentos de proteção individual (EPIs).
2. Desconexão do Sistema: Desconecte a válvula do sistema em funcionamento para evitar quaisquer riscos durante o processo de calibração. Sigam as recomendações do fabricante para segurança.
3. Verificação Visual: Inspecione a válvula quanto a sinais de desgaste ou danos. Certifique-se de que não haja obstruções que possam afetar seu funcionamento.
4. Montagem do Manômetro: Conecte um manômetro calibrado à válvula para monitorar as pressões em tempo real durante a calibração. É fundamental que o manômetro esteja em boas condições e devidamente calibrado.
5. Ajuste da Pressão: Aumente a pressão de forma controlada até atingir o ponto de ajuste especificado pela válvula de segurança. Observe as leituras no manômetro para garantir que a válvula abra na pressão correta.
6. Testes de Funcionamento: Após o ajuste, realize testes de funcionamento da válvula. Isso inclui a abertura e o fechamento da válvula para garantir que ela está reagindo corretamente à pressão aplicada.
7. Documentação: Registre todos os dados da calibração, incluindo pressões testadas e resultados obtidos. A documentação é importante para auditorias futuras e para garantir a conformidade com as normas.
8. Reinstalação: Finalmente, desconecte o manômetro e reinstale a válvula no sistema, certificando-se de que todas as conexões estejam seguras. Realize uma última verificação para garantir que tudo esteja em ordem antes de retomar o funcionamento.
Erros Comuns na Calibração
Durante o processo de calibração de válvulas de segurança, é comum cometer alguns erros que podem comprometer a eficácia da operação. Reconhecer esses erros é fundamental para garantir a segurança e a funcionalidade do sistema.
1. Não Seguir as Especificações do Fabricante: Cada válvula de segurança possui especificações e requisitos próprios. Ignorar essas orientações pode resultar em calibrações inadequadas, levando a falhas no funcionamento.
2. Falta de Verificação dos Instrumentos de Medição: Utilizar manômetros ou outros instrumentos de medição que não estão calibrados corretamente pode causar leituras imprecisas. Isso afetará diretamente a calibração da válvula, comprometendo sua segurança.
3. Ambiente Inadequado para Calibração: Realizar a calibração em um ambiente inseguro ou não controlado pode levar a acidentes. Além disso, condições ambientais adversas, como temperaturas extremas, podem afetar a precisão do processo.
4. Pressão de Ajuste Inadequada: A calibração deve ser realizada na pressão correta. Ajustar a válvula para abrir em uma pressão que não corresponde às especificações pode resultar em falhas em situações de emergência.
5. Desconsiderar a Manutenção Prévia: Não realizar a inspeção e manutenção das válvulas antes da calibração pode levar a problemas não detectados, como desvio de peças ou desgaste, que afetarão a operação da válvula.
6. Negligenciar a Documentação: Falhar na documentação do processo de calibração pode resultar em dificuldades futuras durante auditorias ou revisões. A falta de registros pode levar a questionamentos sobre a eficácia dos processos de segurança.
7. Saltar Etapas do Processo: A pressa em concluir a calibração pode levar a saltar etapas críticas, resultando em um processo incompleto ou inadequado. É fundamental seguir todas as etapas de forma meticulosa e cuidadosa.
Reconhecer e evitar esses erros comuns é essencial para garantir a eficácia e a segurança das válvulas de segurança. Uma calibração adequada não apenas protege as instalações, mas também assegura a segurança de todos os envolvidos.
Frequência Recomendada para Calibração
A frequência recomendada para a calibração de válvulas de segurança é um aspecto crucial para garantir sua eficácia e segurança em sistemas industriais. Determinar um cronograma adequado pode prevenir falhas e acidentes.
1. Normas e Regulamentações: Muitas indústrias estão sujeitas a normas e regulamentações que definem a frequência mínima para a calibração de válvulas de segurança. É essencial estar ciente dessas diretrizes e segui-las rigorosamente.
2. Calibração Anual: Em geral, uma calibração anual é considerada uma prática padrão na maioria das indústrias. Este intervalo permite detectar desgastes e desajustes, garantindo que as válvulas respondam corretamente em situações de emergência.
3. Mudanças no Ambiente Operacional: Caso haja alterações significativas no ambiente operacional, como mudanças de pressão ou temperatura, pode ser necessário realizar calibrações mais frequentes. Essas condições podem afetar a precisão das válvulas.
4. Após Manutenção ou Reparos: Quando uma válvula é submetida a manutenção ou reparos, uma calibração deve ser realizada imediatamente. Isso assegura que a válvula esteja funcionando corretamente após ajustes ou trocas de componentes.
5. Antes de Atividades Críticas: Em situações em que a segurança é primordial, como antes de atividades que envolvam riscos elevados, recomenda-se realizar uma calibração prévia. Isso garante que as válvulas estarão operando de forma segura durante essas atividades.
6. Registros da Performance: É fundamental manter registros detalhados de cada calibração. Esses dados ajudam a identificar padrões que possam indicar a necessidade de calibrações mais frequentes, com base em desempenho inconsistentes.
A definição da frequência ideal para a calibração de válvulas de segurança depende de uma combinação de normas, práticas recomendadas e características operacionais específicas. Ao seguir essas diretrizes, as empresas podem maximizar a segurança e a eficiência de seus sistemas.
Ferramentas Necessárias para Calibração
A calibração de válvulas de segurança exige o uso de ferramentas adequadas para garantir precisão e segurança durante o processo. Ter os equipamentos certos à disposição pode facilitar o trabalho e garantir resultados eficazes.
1. Manômetro Calibrado: Um manômetro calibrado é essencial para medir a pressão em tempo real durante a calibração. Isso garante que a válvula abra na pressão correta e permite monitorar seu desempenho.
2. Chaves de Fenda e Chaves de Boca: Ferramentas básicas como chaves de fenda e chaves de boca são necessárias para desmontar e montar a válvula, bem como para ajustar componentes durante o processo de calibração.
3. Multímetro: Um multímetro é útil para verificar conexões elétricas e assegurar que todos os componentes da válvula, especialmente as válvulas eletrônicas, estejam funcionando corretamente. Isso pode ajudar a evitar problemas elétricos que afetam a calibração.
4. Equipamentos de Proteção Individual (EPIs): É fundamental utilizar EPIs, como luvas, óculos de proteção e protetores auditivos, para garantir a segurança do técnico durante a calibração. A proteção contra riscos mecânicos e químicos deve ser uma prioridade.
5. Ferramentas de Lubrificação: Lubrificantes apropriados são necessários para garantir que as partes móveis da válvula funcionem suavemente. O uso de lubrificante nas partes críticas pode melhorar a eficiência e a durabilidade da válvula.
6. Dispositivos de Montagem: Em alguns casos, dispositivos de montagem adicionais podem ser necessários para segurar a válvula durante a calibração. Isso ajuda a prevenir movimentos indesejados que podem afetar a precisão do processo.
7. Documentação e Registro: Embora não seja uma ferramenta física, a documentação adequada e um sistema para registrar os resultados da calibração são essenciais. Este registro ajuda a rastrear a conformidade e a eficácia da calibração ao longo do tempo.
Ter essas ferramentas à disposição e utilizá-las corretamente pode aumentar significativamente a precisão e a segurança da calibração de válvulas de segurança. Isso não apenas protege os operadores, mas também assegura a integridade dos sistemas industriais.
Normas e Regulamentações sobre Calibração de Válvulas
As normas e regulamentações sobre a calibração de válvulas de segurança são fundamentais para garantir a segurança e a eficácia em ambientes industriais. Essas diretrizes ajudam a prevenir acidentes e a assegurar que os equipamentos operem de acordo com os padrões estabelecidos.
1. Normas da ABNT: A Associação Brasileira de Normas Técnicas (ABNT) estabelece normas específicas para a calibração de instrumentos de medição e válvulas de segurança. É essencial que os profissionais conheçam e sigam essas normas para garantir a conformidade.
2. Normas ANSI/ISA: As normas da American National Standards Institute (ANSI) e da International Society for Automation (ISA) oferecem diretrizes abrangentes para a calibração de válvulas em sistemas industriais, enfatizando a importância de procedimentos e documentação adequados.
3. Diretivas da OSHA: Nos Estados Unidos, a Occupational Safety and Health Administration (OSHA) regula a segurança no trabalho, incluindo a necessidade de calibração adequada de válvulas de segurança em locais de trabalho para proteger os funcionários e minimizar riscos.
4. Requisitos de Certificação ISO: O cumprimento da norma ISO 9001, que trata de sistemas de gestão da qualidade, geralmente inclui a necessidade de calibrações regulares e documentação precisa dos procedimentos. Isso é vital para manter a certificação e assegurar a qualidade dos produtos e serviços.
5. Regulamentações Locais: Dependendo da jurisdição, várias regulamentações locais podem exigir calibrações em intervalos específicos ou após eventos significativos, como manutenções e alterações na operação. É imprescindível que as empresas estejam cientes das leis aplicáveis na sua região.
6. Auditorias e Inspeções: As empresas também podem estar sujeitas a auditorias regulares que avaliam o cumprimento das normas de calibração. A falta de conformidade pode resultar em sanções legais, multas e até mesmo paralisação de operações.
7. Treinamento e Capacitação: As normas frequentemente exigem que os técnicos responsáveis pela calibração sejam adequadamente treinados e certificados. Isso garante que os procedimentos sejam realizados corretamente e com segurança.
Cumprir com as normas e regulamentações sobre a calibração de válvulas de segurança é imprescindível para qualquer instalação industrial. Isso não só assegura a conformidade legal, mas também promove um ambiente de trabalho seguro e eficiente.
A calibração de válvulas de segurança é um aspecto crucial na manutenção da segurança e eficiência nos sistemas industriais. Através de um processo sistemático e a adoção de boas práticas, é possível garantir que esses dispositivos operem de forma confiável e eficaz.
Identificar a importância da calibração, entender os passos necessários, evitar erros comuns e seguir as regulamentações são fatores que contribuem diretamente para a segurança dos trabalhadores e a integridade das instalações.
Além disso, a utilização das ferramentas adequadas e o cumprimento das normas vigentes não apenas ajudam a prevenir acidentes, mas também promovem uma cultura de responsabilidade e segurança no ambiente de trabalho.
Em resumo, ao investir tempo e recursos na calibração de válvulas de segurança, as empresas não somente atendem a exigências legais, mas também asseguram a continuidade e a eficiência de suas operações, criando um ambiente de trabalho mais seguro para todos.