Calibração de Válvulas de Segurança Precisão
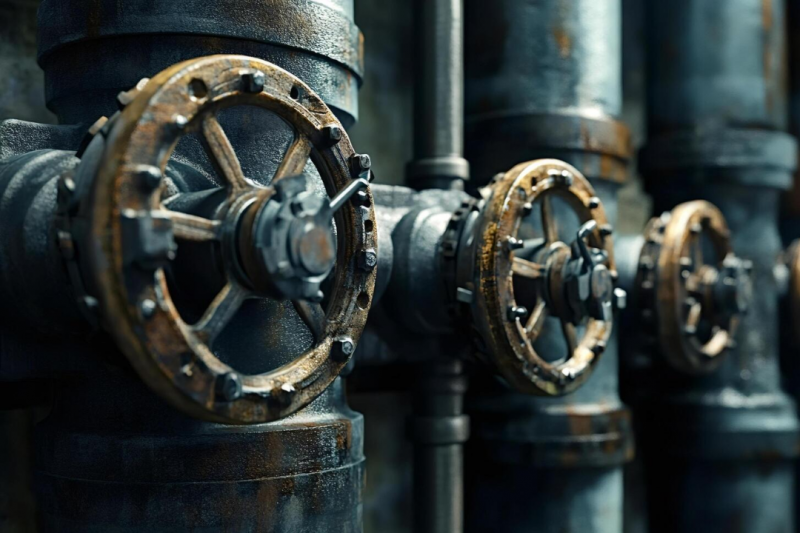
Por: Thiago - 30 de Junho de 2025
A calibração de válvulas de segurança é um processo crucial para garantir a eficiência e a segurança em sistemas industriais. Essas válvulas desempenham um papel vital na proteção de equipamentos e na prevenção de acidentes, assegurando que a pressão não exceda limites seguros. Neste artigo, abordaremos a importância da calibração, os passos necessários para realizá-la corretamente e os erros comuns que devem ser evitados, além de dicas para a manutenção regular dessas válvulas.
Importância da Calibração de Válvulas de Segurança em Sistemas Industriais
A calibração de válvulas de segurança é um aspecto fundamental na operação de sistemas industriais, especialmente em setores que lidam com fluidos pressurizados, como petróleo, gás, química e energia. Essas válvulas são projetadas para liberar pressão excessiva, evitando assim falhas catastróficas que podem resultar em danos a equipamentos, perdas financeiras e, mais importante, riscos à segurança dos trabalhadores e do meio ambiente.
Um dos principais motivos para a calibração regular das válvulas de segurança é garantir que elas funcionem de maneira eficaz e dentro dos parâmetros estabelecidos. Quando uma válvula de segurança não está calibrada corretamente, pode não abrir na pressão adequada, resultando em um aumento perigoso da pressão no sistema. Isso pode levar a explosões, vazamentos e outros incidentes graves. Portanto, a calibração é essencial para assegurar que as válvulas respondam de forma confiável às condições de operação.
Além disso, a calibração de válvulas de segurança é uma exigência normativa em muitos setores. As normas de segurança, como as estabelecidas pela American Society of Mechanical Engineers (ASME) e pela Occupational Safety and Health Administration (OSHA), exigem que as válvulas de segurança sejam testadas e calibradas regularmente. O não cumprimento dessas normas pode resultar em penalidades legais e comprometer a integridade da operação industrial.
Outro ponto a ser considerado é a eficiência operacional. Válvulas de segurança que não estão calibradas corretamente podem causar interrupções na produção, levando a paradas não programadas e perda de produtividade. A calibração regular ajuda a minimizar esses riscos, garantindo que as válvulas funcionem de maneira otimizada e contribuam para a eficiência geral do sistema.
Além disso, a calibração de válvulas de segurança está diretamente relacionada à manutenção preventiva. A realização de calibrações regulares permite identificar problemas potenciais antes que se tornem críticos. Isso não apenas aumenta a vida útil das válvulas, mas também reduz os custos de manutenção a longo prazo. A manutenção preditiva, que inclui a calibração, é uma estratégia eficaz para evitar falhas inesperadas e garantir a continuidade das operações.
É importante ressaltar que a calibração deve ser realizada por profissionais qualificados, que compreendam as especificações técnicas das válvulas e as condições de operação do sistema. A formação adequada, como a oferecida no curso operador de caldeira, é essencial para garantir que os operadores e técnicos estejam aptos a realizar calibrações precisas e seguras.
Além da segurança e eficiência, a calibração de válvulas de segurança também desempenha um papel importante na proteção ambiental. Válvulas que falham podem resultar em vazamentos de substâncias perigosas, causando danos ao meio ambiente e à saúde pública. A calibração regular ajuda a prevenir esses incidentes, contribuindo para a sustentabilidade e a responsabilidade ambiental das operações industriais.
Por fim, a calibração de válvulas de segurança é um componente crítico da cultura de segurança dentro de uma organização. Promover a conscientização sobre a importância da calibração e garantir que todos os funcionários estejam envolvidos no processo é fundamental para criar um ambiente de trabalho seguro. Isso inclui treinamentos regulares e a implementação de procedimentos operacionais padrão que enfatizem a calibração e a manutenção das válvulas de segurança.
Em resumo, a calibração de válvulas de segurança em sistemas industriais é vital para garantir a segurança, eficiência e conformidade normativa. Através de práticas de calibração regulares, as empresas podem proteger seus ativos, garantir a segurança dos trabalhadores e minimizar o impacto ambiental. Investir na calibração e na formação adequada dos profissionais envolvidos é uma estratégia inteligente que traz benefícios a longo prazo para qualquer operação industrial.
Passo a Passo para Realizar a Calibração de Válvulas de Segurança
A calibração de válvulas de segurança é um processo essencial para garantir que esses dispositivos funcionem corretamente e mantenham a segurança em sistemas industriais. A seguir, apresentamos um guia passo a passo para realizar a calibração de válvulas de segurança, assegurando que todas as etapas sejam seguidas de maneira adequada e segura.
1. Preparação e Planejamento
Antes de iniciar o processo de calibração, é fundamental realizar um planejamento cuidadoso. Isso inclui a revisão das especificações do fabricante da válvula de segurança, bem como a coleta de todas as ferramentas e equipamentos necessários. É importante ter em mãos manômetros calibrados, chaves de fenda, chaves inglesas e outros instrumentos que possam ser necessários durante o processo. Para garantir a precisão das medições, a calibração de manômetros deve ser realizada previamente.
2. Desligamento do Sistema
Antes de realizar qualquer trabalho na válvula de segurança, é crucial desligar o sistema em que ela está instalada. Isso garante a segurança do operador e evita acidentes. Certifique-se de que a pressão no sistema esteja completamente liberada e que não haja fluidos perigosos presentes. Utilize os procedimentos de bloqueio e etiquetagem (Lockout/Tagout) para garantir que o sistema não seja reativado acidentalmente durante a calibração.
3. Inspeção Visual da Válvula
Após o desligamento do sistema, realize uma inspeção visual da válvula de segurança. Verifique se há sinais de desgaste, corrosão ou danos. Certifique-se de que todos os componentes estejam em boas condições e que não haja vazamentos. Se a válvula apresentar problemas visíveis, é recomendável realizar reparos antes de prosseguir com a calibração.
4. Conexão do Manômetro
Com a válvula de segurança em boas condições, conecte um manômetro calibrado à entrada da válvula. O manômetro deve ser capaz de medir a pressão máxima que a válvula deve suportar. Certifique-se de que as conexões estejam firmes e que não haja vazamentos. A precisão do manômetro é crucial para garantir que a calibração seja realizada corretamente.
5. Ajuste da Pressão de Atuação
Uma vez que o manômetro esteja conectado, comece a aumentar a pressão no sistema lentamente. Isso pode ser feito utilizando uma bomba de pressão ou outro dispositivo apropriado. Monitore a pressão no manômetro enquanto a pressão aumenta. A válvula de segurança deve abrir em uma pressão específica, conforme especificado pelo fabricante. Quando a válvula abrir, anote a pressão indicada no manômetro.
6. Verificação da Pressão de Fechamento
Após a válvula abrir, continue a aumentar a pressão até que a válvula feche novamente. A pressão em que a válvula fecha é conhecida como pressão de fechamento. Essa informação é igualmente importante e deve ser registrada. A diferença entre a pressão de abertura e a pressão de fechamento deve estar dentro dos limites especificados pelo fabricante.
7. Ajustes Necessários
Se a pressão de abertura ou fechamento não estiver dentro das especificações, ajustes devem ser feitos. Isso pode envolver a modificação de um parafuso de ajuste na válvula, que altera a pressão em que a válvula abre ou fecha. Após realizar os ajustes, repita os passos 5 e 6 para verificar se as novas configurações estão corretas.
8. Documentação dos Resultados
Uma vez que a calibração tenha sido concluída com sucesso, é importante documentar todos os resultados. Isso inclui a pressão de abertura, a pressão de fechamento e quaisquer ajustes realizados. A documentação deve ser mantida em registros de manutenção, pois é essencial para auditorias e conformidade com normas de segurança.
9. Reinstalação e Testes Finais
Após a calibração e a documentação, desconecte o manômetro e reinstale a válvula de segurança no sistema. Certifique-se de que todas as conexões estejam firmes e que não haja vazamentos. Em seguida, reative o sistema e monitore a válvula de segurança durante a operação inicial para garantir que ela funcione corretamente.
10. Manutenção Regular
A calibração de válvulas de segurança não deve ser um evento isolado. É fundamental estabelecer um cronograma de calibração regular, conforme recomendado pelo fabricante e pelas normas de segurança aplicáveis. A manutenção preventiva ajuda a garantir que as válvulas permaneçam em boas condições e funcionem de maneira eficaz ao longo do tempo.
Seguir este passo a passo para a calibração de válvulas de segurança é essencial para garantir a segurança e a eficiência em sistemas industriais. A calibração adequada não apenas protege os equipamentos, mas também assegura a segurança dos trabalhadores e a conformidade com as normas regulatórias. Portanto, investir tempo e recursos na calibração de válvulas de segurança é uma prática inteligente e necessária em qualquer operação industrial.
Erros Comuns na Calibração de Válvulas de Segurança e Como Evitá-los
A calibração de válvulas de segurança é um processo crítico para garantir a segurança e a eficiência em sistemas industriais. No entanto, existem diversos erros que podem ocorrer durante esse processo, comprometendo a eficácia das válvulas e colocando em risco a segurança dos operadores e a integridade dos equipamentos. A seguir, discutiremos os erros mais comuns na calibração de válvulas de segurança e como evitá-los.
1. Falta de Planejamento Adequado
Um dos erros mais frequentes é a falta de planejamento antes de iniciar a calibração. Muitas vezes, os operadores começam o processo sem revisar as especificações do fabricante ou sem ter as ferramentas necessárias à mão. Isso pode levar a medições imprecisas e a um processo de calibração ineficaz. Para evitar esse erro, é fundamental elaborar um plano detalhado que inclua a revisão das especificações da válvula, a coleta de ferramentas e equipamentos adequados e a definição de um cronograma para a calibração.
2. Não Realizar a Calibração em Condições Ideais
A calibração deve ser realizada em condições ideais para garantir resultados precisos. Isso significa que a temperatura, a pressão e outros fatores ambientais devem estar dentro dos limites recomendados. Realizar a calibração em condições adversas pode resultar em leituras imprecisas. Para evitar esse erro, sempre verifique as condições do ambiente antes de iniciar a calibração e, se necessário, aguarde até que as condições sejam adequadas.
3. Ignorar a Importância da Memória de Cálculo
A memória de cálculo é uma ferramenta essencial para garantir que todos os parâmetros e resultados da calibração sejam registrados de forma precisa. Ignorar essa etapa pode levar a erros na documentação e na análise dos resultados. É importante manter uma memória de cálculo detalhada, que inclua todas as medições, ajustes realizados e observações durante o processo de calibração. Isso não apenas ajuda a evitar erros, mas também fornece um histórico valioso para futuras calibrações e auditorias.
4. Não Realizar Inspeções Visuais
Antes de iniciar a calibração, é crucial realizar uma inspeção visual da válvula de segurança. Ignorar essa etapa pode resultar em falhas não detectadas que comprometam a calibração. Verifique se há sinais de desgaste, corrosão ou danos. Se a válvula não estiver em boas condições, a calibração pode ser inútil. Para evitar esse erro, sempre faça uma inspeção visual detalhada antes de iniciar o processo de calibração.
5. Uso de Equipamentos Não Calibrados
Utilizar manômetros ou outros instrumentos de medição que não estejam calibrados pode levar a resultados imprecisos. Isso compromete a calibração da válvula de segurança e pode resultar em falhas no sistema. Para evitar esse erro, sempre verifique se os instrumentos de medição estão calibrados e em boas condições antes de usá-los. Se necessário, realize a calibração dos instrumentos antes de iniciar o processo.
6. Não Registrar os Resultados Corretamente
Após a calibração, é fundamental registrar todos os resultados de forma precisa. Muitos operadores cometem o erro de não documentar as medições ou de fazê-lo de maneira inadequada. Isso pode dificultar a análise futura e a verificação da conformidade com as normas de segurança. Para evitar esse erro, estabeleça um sistema de documentação claro e consistente, garantindo que todos os resultados sejam registrados de forma precisa e acessível.
7. Ignorar a Necessidade de Treinamento
A calibração de válvulas de segurança deve ser realizada por profissionais qualificados e treinados. Ignorar a necessidade de treinamento pode resultar em erros graves durante o processo. É fundamental que os operadores e técnicos recebam formação adequada sobre as especificações das válvulas, os procedimentos de calibração e as normas de segurança. Para evitar esse erro, invista em programas de treinamento e capacitação para sua equipe.
8. Não Realizar Calibrações Regulares
Um erro comum é não estabelecer um cronograma de calibração regular. Muitas empresas realizam a calibração apenas quando um problema é identificado, o que pode resultar em falhas não detectadas. A calibração deve ser parte de um programa de manutenção preventiva, com intervalos regulares definidos com base nas recomendações do fabricante e nas normas de segurança. Para evitar esse erro, crie um cronograma de calibração e mantenha registros das calibrações realizadas.
9. Falta de Comunicação entre as Equipes
A comunicação inadequada entre as equipes de operação e manutenção pode levar a erros na calibração. Se as informações sobre as condições do sistema ou as especificações da válvula não forem compartilhadas, isso pode resultar em medições imprecisas. Para evitar esse erro, estabeleça canais de comunicação claros entre as equipes e promova a troca de informações relevantes antes de realizar a calibração.
10. Não Realizar Testes Finais
Após a calibração, é essencial realizar testes finais para garantir que a válvula de segurança esteja funcionando corretamente. Ignorar essa etapa pode resultar em falhas não detectadas que comprometam a segurança do sistema. Para evitar esse erro, sempre teste a válvula após a calibração, monitorando seu desempenho e verificando se ela abre e fecha nas pressões corretas.
Em resumo, a calibração de válvulas de segurança é um processo crítico que deve ser realizado com atenção e cuidado. Evitar os erros comuns mencionados acima é fundamental para garantir a eficácia das válvulas e a segurança dos sistemas industriais. Investir em planejamento, treinamento e documentação adequada ajudará a minimizar riscos e a garantir que as válvulas de segurança funcionem de maneira confiável e eficiente.
Manutenção e Verificação Regular das Válvulas de Segurança
A manutenção e verificação regular das válvulas de segurança são essenciais para garantir a segurança e a eficiência em sistemas industriais. Essas válvulas desempenham um papel crucial na proteção de equipamentos e na prevenção de acidentes, liberando pressão excessiva e evitando falhas catastróficas. Neste artigo, discutiremos a importância da manutenção regular, as melhores práticas e os procedimentos recomendados para garantir que as válvulas de segurança funcionem de maneira eficaz.
1. Importância da Manutenção Regular
A manutenção regular das válvulas de segurança é fundamental para assegurar que elas operem dentro dos parâmetros especificados pelo fabricante. Com o tempo, as válvulas podem sofrer desgaste, corrosão e outros danos que podem comprometer seu funcionamento. A falta de manutenção pode resultar em falhas que não apenas danificam os equipamentos, mas também colocam em risco a segurança dos trabalhadores e do meio ambiente. Portanto, realizar verificações e manutenções periódicas é uma prática essencial para qualquer operação industrial.
2. Frequência das Manutenções
A frequência das manutenções deve ser determinada com base nas recomendações do fabricante, nas normas de segurança aplicáveis e nas condições de operação do sistema. Em geral, é recomendável realizar inspeções visuais e testes de funcionamento a cada seis meses. No entanto, em ambientes de alta pressão ou em sistemas críticos, pode ser necessário aumentar a frequência das manutenções. É importante estabelecer um cronograma de manutenção que leve em consideração esses fatores e que seja seguido rigorosamente.
3. Inspeção Visual
A primeira etapa da manutenção regular é a inspeção visual das válvulas de segurança. Durante essa inspeção, os operadores devem verificar se há sinais de desgaste, corrosão, vazamentos ou danos visíveis. É importante observar as condições gerais da válvula, incluindo as conexões e os suportes. Se forem identificados problemas durante a inspeção, a válvula deve ser retirada de serviço e reparos devem ser realizados imediatamente.
4. Testes de Funcionamento
Além da inspeção visual, é fundamental realizar testes de funcionamento das válvulas de segurança. Isso envolve a aplicação de pressão ao sistema para verificar se a válvula abre e fecha nas pressões corretas. Os testes devem ser realizados de acordo com as especificações do fabricante e devem ser documentados para garantir a conformidade com as normas de segurança. Se a válvula não funcionar corretamente durante os testes, ajustes ou reparos devem ser feitos antes que a válvula seja reinstalada no sistema.
5. Registro e Documentação
Manter registros detalhados de todas as manutenções e verificações realizadas é uma prática essencial. Esses registros devem incluir informações sobre as inspeções visuais, os testes de funcionamento, os ajustes realizados e quaisquer problemas identificados. A documentação adequada não apenas ajuda a garantir a conformidade com as normas de segurança, mas também fornece um histórico valioso para futuras manutenções e auditorias. É recomendável utilizar um sistema de gerenciamento de manutenção que facilite o registro e a consulta dessas informações.
6. Treinamento da Equipe
Para garantir que a manutenção e verificação das válvulas de segurança sejam realizadas de maneira eficaz, é fundamental que a equipe envolvida esteja devidamente treinada. O Treinamento nr 13 é uma excelente oportunidade para capacitar os operadores e técnicos sobre as melhores práticas de manutenção e segurança. O treinamento deve incluir informações sobre as especificações das válvulas, os procedimentos de manutenção e as normas de segurança aplicáveis. Investir na formação da equipe é uma estratégia inteligente que contribui para a segurança e a eficiência operacional.
7. Manutenção Preditiva
A manutenção preditiva é uma abordagem que visa identificar problemas potenciais antes que se tornem críticos. Isso pode ser feito por meio de monitoramento contínuo das condições das válvulas de segurança, utilizando tecnologias como sensores e sistemas de automação. A manutenção preditiva permite que as empresas realizem intervenções programadas, minimizando o tempo de inatividade e os custos associados a falhas inesperadas. Implementar um programa de manutenção preditiva pode ser uma maneira eficaz de garantir a confiabilidade das válvulas de segurança.
8. Substituição de Componentes
Com o tempo, alguns componentes das válvulas de segurança podem se desgastar e precisar de substituição. É importante estar atento a sinais de desgaste e realizar a troca de peças conforme necessário. A substituição de componentes deve ser feita de acordo com as recomendações do fabricante e deve ser documentada adequadamente. Isso garante que as válvulas continuem a operar de maneira eficaz e segura.
9. Conformidade com Normas e Regulamentações
A manutenção e verificação das válvulas de segurança devem estar em conformidade com as normas e regulamentações aplicáveis. Isso inclui normas de segurança, como as estabelecidas pela American Society of Mechanical Engineers (ASME) e pela Occupational Safety and Health Administration (OSHA). A conformidade com essas normas é fundamental para garantir a segurança dos trabalhadores e a integridade dos sistemas industriais. As empresas devem estar cientes das regulamentações e garantir que suas práticas de manutenção estejam alinhadas com elas.
10. Revisão e Melhoria Contínua
Por fim, é importante que as empresas realizem revisões periódicas de seus programas de manutenção e verificação das válvulas de segurança. Isso inclui a análise dos registros de manutenção, a avaliação da eficácia das práticas atuais e a identificação de oportunidades de melhoria. A melhoria contínua é essencial para garantir que as válvulas de segurança permaneçam em boas condições e que a segurança operacional seja mantida ao longo do tempo.
Em resumo, a manutenção e verificação regular das válvulas de segurança são essenciais para garantir a segurança e a eficiência em sistemas industriais. Através de inspeções visuais, testes de funcionamento, documentação adequada e treinamento da equipe, as empresas podem minimizar riscos e garantir que suas válvulas de segurança operem de maneira confiável. Investir em práticas de manutenção eficazes é uma estratégia inteligente que traz benefícios a longo prazo para qualquer operação industrial.
Em conclusão, a calibração e a manutenção regular das válvulas de segurança são fundamentais para garantir a segurança e a eficiência em sistemas industriais. Através de práticas adequadas, como inspeções visuais, testes de funcionamento e documentação rigorosa, é possível minimizar riscos e assegurar que essas válvulas operem de maneira confiável. Além disso, investir em treinamento e capacitação da equipe é essencial para que todos os envolvidos compreendam a importância dessas práticas e possam executá-las corretamente. Ao seguir as diretrizes apresentadas, as empresas não apenas protegem seus equipamentos e colaboradores, mas também promovem um ambiente de trabalho mais seguro e eficiente.