Calibração de válvulas de segurança é essencial para garantir a eficiência e a segurança do seu sistema industrial
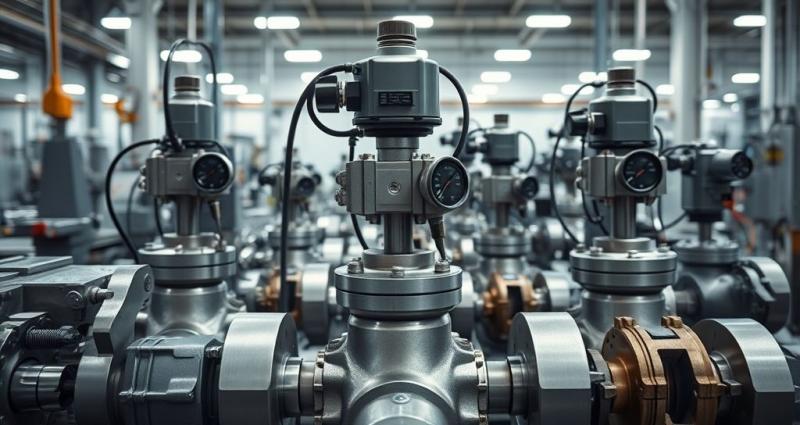
Por: Thiago - 17 de Abril de 2025
A calibração de válvulas de segurança é um processo fundamental para garantir a eficiência e a segurança em sistemas industriais. Essas válvulas desempenham um papel crucial na proteção de equipamentos e na prevenção de acidentes, assegurando que a pressão não exceda limites seguros. Neste artigo, abordaremos a importância da calibração, os passos necessários para realizá-la corretamente e os erros comuns que devem ser evitados, além de dicas para a manutenção regular dessas válvulas.
Importância da Calibração de Válvulas de Segurança na Indústria
A calibração de válvulas de segurança é um aspecto crítico na operação de sistemas industriais, especialmente em setores que lidam com fluidos pressurizados, como petróleo, gás, química e energia. Essas válvulas são projetadas para abrir automaticamente quando a pressão atinge um nível perigoso, evitando assim explosões e outros acidentes graves. Portanto, garantir que essas válvulas estejam calibradas corretamente é essencial para a segurança dos trabalhadores e a integridade das instalações.
Um dos principais motivos para a calibração regular das válvulas de segurança é a prevenção de falhas. Com o tempo, as válvulas podem sofrer desgaste devido a fatores como corrosão, sedimentação e variações de temperatura. Esses fatores podem afetar a precisão da válvula, fazendo com que ela não abra na pressão correta. Se uma válvula de segurança falhar em abrir quando necessário, as consequências podem ser catastróficas, resultando em danos ao equipamento, ferimentos aos funcionários e até mesmo fatalidades.
Além da segurança, a calibração de válvulas de segurança também impacta a eficiência operacional. Válvulas que não estão calibradas corretamente podem causar flutuações de pressão indesejadas, levando a um desempenho ineficiente do sistema. Isso pode resultar em paradas não programadas, aumento dos custos operacionais e perda de produtividade. Portanto, a calibração não é apenas uma questão de segurança, mas também uma estratégia para otimizar a operação industrial.
Outro aspecto importante a considerar é a conformidade regulatória. Muitas indústrias são obrigadas a seguir normas e regulamentos rigorosos que exigem a calibração regular de válvulas de segurança. A não conformidade pode resultar em multas significativas, processos legais e danos à reputação da empresa. Portanto, manter um programa de calibração adequado não só garante a segurança, mas também ajuda a evitar complicações legais.
A calibração de válvulas de segurança deve ser realizada por profissionais qualificados que compreendam as especificações do equipamento e as normas aplicáveis. Esses especialistas utilizam equipamentos de medição precisos para garantir que as válvulas estejam funcionando dentro dos parâmetros estabelecidos. Além disso, a documentação adequada do processo de calibração é fundamental para auditorias e verificações futuras.
Um aspecto frequentemente negligenciado é a importância da calibração de manômetros associados às válvulas de segurança. Os manômetros são instrumentos que medem a pressão dentro de um sistema e, se não estiverem calibrados corretamente, podem fornecer leituras imprecisas. Isso pode levar a decisões erradas sobre a operação das válvulas de segurança. Portanto, a calibração de manômetros deve ser parte integrante do programa de calibração de válvulas de segurança, garantindo que todos os componentes do sistema estejam funcionando em harmonia.
Além disso, a calibração deve ser realizada em intervalos regulares, que podem variar dependendo do tipo de válvula, do ambiente de operação e das recomendações do fabricante. Muitas empresas adotam um cronograma de calibração preventiva, que ajuda a identificar problemas antes que se tornem críticos. Essa abordagem proativa não só melhora a segurança, mas também reduz os custos de manutenção a longo prazo.
Em resumo, a calibração de válvulas de segurança é uma prática essencial na indústria que não deve ser subestimada. Ela garante a segurança dos trabalhadores, a eficiência operacional e a conformidade regulatória. Investir em um programa de calibração robusto e em profissionais qualificados é fundamental para proteger tanto os ativos da empresa quanto a vida dos funcionários. Com a calibração adequada, as indústrias podem operar com confiança, sabendo que suas válvulas de segurança estão prontas para agir quando necessário.
Passos para Realizar a Calibração de Válvulas de Segurança
A calibração de válvulas de segurança é um processo crítico que deve ser realizado com precisão para garantir a segurança e a eficiência dos sistemas industriais. A seguir, apresentamos um guia passo a passo para realizar a calibração de válvulas de segurança, abordando desde a preparação até a verificação final.
1. Preparação e Planejamento
Antes de iniciar o processo de calibração, é fundamental realizar um planejamento adequado. Isso inclui a identificação das válvulas que precisam ser calibradas, a definição do cronograma e a alocação de recursos necessários, como ferramentas e equipamentos. Além disso, é importante revisar a documentação técnica das válvulas, que pode incluir especificações do fabricante e normas aplicáveis.
Durante essa fase, também é essencial garantir que a equipe envolvida na calibração esteja devidamente treinada e ciente dos procedimentos a serem seguidos. A segurança deve ser a prioridade, e todos os profissionais devem usar Equipamentos de Proteção Individual (EPIs) adequados.
2. Desconexão e Isolamento do Sistema
Antes de realizar a calibração, é necessário desconectar a válvula de segurança do sistema. Isso envolve o isolamento da válvula, garantindo que não haja pressão no sistema durante o processo. O isolamento deve ser feito de acordo com os procedimentos de segurança da empresa, e todos os envolvidos devem ser informados sobre a desativação temporária da válvula.
Uma vez que a válvula esteja isolada, é importante verificar se não há pressão residual. Isso pode ser feito utilizando manômetros ou outros dispositivos de medição. A segurança da equipe é fundamental, e qualquer erro nesta etapa pode resultar em acidentes graves.
3. Inspeção Visual da Válvula
Com a válvula desconectada, o próximo passo é realizar uma inspeção visual detalhada. Essa inspeção deve incluir a verificação de sinais de desgaste, corrosão ou danos visíveis. Componentes como assentos, molas e selos devem ser examinados para garantir que estejam em boas condições de funcionamento.
Se forem identificados problemas durante a inspeção, é recomendável realizar os reparos necessários antes de prosseguir com a calibração. A manutenção preventiva é uma parte importante do processo, pois garante que a válvula funcione corretamente após a calibração.
4. Calibração da Válvula
A calibração propriamente dita envolve a aplicação de pressão à válvula de segurança para verificar se ela abre e fecha nos pontos de pressão especificados. Para isso, um equipamento de calibração, como um manômetro calibrado, deve ser utilizado. A pressão deve ser aumentada gradualmente até que a válvula atinja seu ponto de abertura, que deve estar de acordo com as especificações do fabricante.
Durante a calibração, é importante registrar todas as leituras e ajustes feitos. Esses dados são essenciais para a memória de cálculo e para futuras referências. A documentação adequada é fundamental para garantir a conformidade com as normas e para auditorias futuras.
Se a válvula não abrir na pressão correta, ajustes devem ser feitos. Isso pode envolver a substituição de componentes ou o ajuste da mola, dependendo do tipo de válvula. Após realizar os ajustes, a calibração deve ser repetida para garantir que a válvula esteja funcionando corretamente.
5. Verificação Final e Testes
Após a calibração, é crucial realizar uma verificação final. Isso inclui testar a válvula em condições de operação reais, se possível. A válvula deve ser reconectada ao sistema e monitorada para garantir que funcione corretamente sob pressão. É importante observar se a válvula abre e fecha conforme esperado e se não há vazamentos.
Além disso, a equipe deve revisar todos os dados coletados durante o processo de calibração e garantir que a documentação esteja completa. Isso inclui a atualização de registros de manutenção e calibração, que são essenciais para a gestão de ativos e para a conformidade regulatória.
6. Reinstalação e Monitoramento Contínuo
Após a verificação final, a válvula de segurança pode ser reinstalada no sistema. É importante garantir que todos os componentes estejam devidamente fixados e que não haja vazamentos. Após a reinstalação, a válvula deve ser monitorada regularmente para garantir que continue a operar dentro dos parâmetros especificados.
O monitoramento contínuo é uma parte vital do processo de calibração. As válvulas de segurança devem ser verificadas periodicamente para garantir que não haja degradação ao longo do tempo. Um programa de manutenção preventiva pode ajudar a identificar problemas antes que se tornem críticos, garantindo a segurança e a eficiência do sistema.
Em resumo, a calibração de válvulas de segurança é um processo que requer atenção cuidadosa e um planejamento adequado. Seguir esses passos garantirá que as válvulas funcionem corretamente, contribuindo para a segurança e a eficiência dos sistemas industriais.
Erros Comuns na Calibração de Válvulas de Segurança
A calibração de válvulas de segurança é um processo crítico que garante a segurança e a eficiência dos sistemas industriais. No entanto, existem diversos erros que podem ocorrer durante esse processo, comprometendo a eficácia das válvulas e colocando em risco a segurança dos trabalhadores e a integridade das instalações. A seguir, discutiremos alguns dos erros mais comuns na calibração de válvulas de segurança e como evitá-los.
1. Falta de Planejamento Adequado
Um dos erros mais frequentes na calibração de válvulas de segurança é a falta de um planejamento adequado. Muitas vezes, as empresas não dedicam tempo suficiente para preparar o processo de calibração, o que pode levar a uma execução apressada e imprecisa. É fundamental que a equipe responsável pela calibração tenha um cronograma claro, defina as etapas do processo e garanta que todos os recursos necessários estejam disponíveis.
Um planejamento eficaz deve incluir a revisão da documentação técnica das válvulas, a definição de responsabilidades e a alocação de tempo suficiente para a realização de cada etapa. Sem um planejamento adequado, o risco de erros aumenta significativamente, o que pode resultar em falhas na operação das válvulas.
2. Ignorar a Inspeção Visual
A inspeção visual das válvulas de segurança é uma etapa crucial que não deve ser negligenciada. Muitos profissionais cometem o erro de pular essa fase, partindo diretamente para a calibração. A inspeção visual permite identificar sinais de desgaste, corrosão ou danos que podem afetar o desempenho da válvula.
Se a válvula não for inspecionada adequadamente, problemas existentes podem ser ignorados, levando a falhas durante a calibração. Portanto, é essencial realizar uma inspeção minuciosa antes de iniciar o processo de calibração, garantindo que a válvula esteja em boas condições de funcionamento.
3. Não Utilizar Equipamentos de Medição Calibrados
Outro erro comum é a utilização de equipamentos de medição que não estão calibrados. Para garantir a precisão da calibração, é fundamental que os manômetros e outros instrumentos de medição estejam em conformidade com as normas e devidamente calibrados. O uso de equipamentos imprecisos pode resultar em leituras erradas, comprometendo a calibração da válvula.
Antes de iniciar o processo de calibração, verifique se todos os instrumentos de medição estão calibrados e em boas condições. Isso garantirá que as leituras sejam precisas e que a válvula funcione corretamente dentro dos parâmetros especificados.
4. Não Registrar Dados Adequadamente
A documentação é uma parte essencial do processo de calibração, e muitos profissionais cometem o erro de não registrar os dados adequadamente. A falta de registros pode dificultar a identificação de problemas futuros e a realização de auditorias. Além disso, a documentação é fundamental para garantir a conformidade com as normas e regulamentos aplicáveis.
É importante manter um registro detalhado de todas as leituras, ajustes e procedimentos realizados durante a calibração. Esses dados devem ser organizados de forma clara e acessível, facilitando a consulta futura e a análise de desempenho das válvulas.
5. Ignorar a Formação e Treinamento da Equipe
A calibração de válvulas de segurança deve ser realizada por profissionais qualificados e treinados. Um erro comum é não investir em formação e treinamento adequados para a equipe responsável pela calibração. A falta de conhecimento sobre os procedimentos corretos pode levar a erros graves durante o processo.
É recomendável que as empresas ofereçam treinamentos regulares para suas equipes, como o Treinamento nr 13, que aborda as normas e práticas de segurança relacionadas à operação de válvulas. A capacitação contínua garante que os profissionais estejam atualizados sobre as melhores práticas e procedimentos, reduzindo o risco de erros durante a calibração.
6. Não Realizar Testes Após a Calibração
Após a calibração, é fundamental realizar testes para verificar se a válvula está funcionando corretamente. Um erro comum é não realizar esses testes, o que pode resultar em falhas não detectadas. A validação do funcionamento da válvula em condições reais é essencial para garantir que ela atenda aos requisitos de segurança e desempenho.
Os testes devem incluir a aplicação de pressão e a verificação do funcionamento da válvula em diferentes condições. Se a válvula não abrir ou fechar conforme esperado, ajustes adicionais podem ser necessários. Ignorar essa etapa pode comprometer a segurança do sistema e aumentar o risco de acidentes.
7. Falta de Manutenção Preventiva
A calibração de válvulas de segurança não deve ser vista como uma atividade isolada, mas sim como parte de um programa de manutenção preventiva mais amplo. Um erro comum é não realizar manutenções regulares nas válvulas, o que pode levar a problemas de desempenho ao longo do tempo. A manutenção preventiva ajuda a identificar e corrigir problemas antes que se tornem críticos, garantindo que as válvulas funcionem corretamente.
As empresas devem estabelecer um cronograma de manutenção que inclua inspeções regulares, limpeza e substituição de componentes conforme necessário. Isso não apenas melhora a segurança, mas também prolonga a vida útil das válvulas e reduz os custos de manutenção a longo prazo.
Em resumo, a calibração de válvulas de segurança é um processo que requer atenção cuidadosa e a adoção de boas práticas. Evitar os erros comuns mencionados acima é fundamental para garantir a segurança e a eficiência dos sistemas industriais. Investir em planejamento, formação da equipe e manutenção preventiva são passos essenciais para garantir que as válvulas de segurança funcionem corretamente e protejam tanto os trabalhadores quanto as instalações.
Manutenção e Verificação Regular das Válvulas de Segurança
A manutenção e verificação regular das válvulas de segurança são práticas essenciais para garantir a segurança e a eficiência dos sistemas industriais. Essas válvulas desempenham um papel crucial na proteção de equipamentos e na prevenção de acidentes, e sua operação adequada é vital para a integridade das instalações e a segurança dos trabalhadores. Neste artigo, abordaremos a importância da manutenção regular, as melhores práticas e os passos a serem seguidos para garantir que as válvulas de segurança funcionem corretamente.
1. Importância da Manutenção Regular
A manutenção regular das válvulas de segurança é fundamental para evitar falhas que podem resultar em acidentes graves. Com o tempo, as válvulas podem sofrer desgaste devido a fatores como corrosão, sedimentação e variações de temperatura. Esses fatores podem afetar a precisão e a funcionalidade das válvulas, tornando-as menos eficazes na proteção contra pressões excessivas.
Além disso, a manutenção regular ajuda a identificar problemas antes que se tornem críticos. A detecção precoce de falhas pode evitar paradas não programadas, danos ao equipamento e custos elevados de reparo. Portanto, investir em um programa de manutenção preventiva é uma estratégia inteligente para garantir a segurança e a eficiência operacional.
2. Frequência da Manutenção
A frequência da manutenção das válvulas de segurança pode variar dependendo de vários fatores, incluindo o tipo de válvula, o ambiente de operação e as recomendações do fabricante. Em geral, é recomendável realizar inspeções e manutenções regulares, que podem ser trimestrais, semestrais ou anuais, conforme a criticidade da aplicação.
Além das manutenções programadas, as válvulas devem ser inspecionadas sempre que houver mudanças nas condições de operação, como alterações na pressão ou temperatura, ou após eventos que possam ter impactado seu funcionamento, como paradas de emergência ou manutenção de outros equipamentos.
3. Procedimentos de Manutenção
Os procedimentos de manutenção das válvulas de segurança devem incluir uma série de etapas para garantir que todas as partes estejam funcionando corretamente. A seguir, apresentamos um guia básico para a manutenção das válvulas de segurança:
- Inspeção Visual: Realize uma inspeção visual detalhada da válvula, verificando se há sinais de desgaste, corrosão ou danos. Preste atenção especial a componentes como assentos, molas e selos.
- Limpeza: Limpe a válvula e seus componentes para remover sujeira, detritos e resíduos que possam afetar seu funcionamento. A limpeza deve ser feita com produtos adequados que não danifiquem os materiais da válvula.
- Teste de Funcionamento: Realize testes de funcionamento para verificar se a válvula abre e fecha corretamente sob pressão. Isso pode incluir a aplicação de pressão controlada e a observação do comportamento da válvula.
- Substituição de Componentes: Se forem identificados problemas durante a inspeção ou os testes, substitua os componentes danificados ou desgastados. Isso pode incluir molas, selos ou assentos.
- Documentação: Registre todas as atividades de manutenção realizadas, incluindo datas, procedimentos e resultados dos testes. A documentação é essencial para auditorias e para garantir a conformidade com as normas.
4. Treinamento da Equipe
Para garantir que a manutenção das válvulas de segurança seja realizada de forma eficaz, é fundamental que a equipe responsável esteja devidamente treinada. O conhecimento sobre os procedimentos corretos de manutenção e calibração é essencial para evitar erros que possam comprometer a segurança.
Investir em treinamentos regulares, como o curso nr 13, que aborda as normas e práticas de segurança relacionadas à operação de válvulas, pode ajudar a capacitar a equipe e garantir que todos estejam atualizados sobre as melhores práticas. A formação contínua é uma parte vital da estratégia de manutenção e segurança.
5. Monitoramento Contínuo
Além da manutenção programada, o monitoramento contínuo das válvulas de segurança é essencial para garantir que elas funcionem corretamente ao longo do tempo. Isso pode incluir a instalação de sistemas de monitoramento que forneçam dados em tempo real sobre a pressão e o desempenho das válvulas.
O monitoramento contínuo permite que as equipes identifiquem rapidamente quaisquer anomalias ou falhas, possibilitando uma resposta rápida e eficaz. Essa abordagem proativa ajuda a evitar problemas antes que se tornem críticos, garantindo a segurança e a eficiência do sistema.
6. Conformidade com Normas e Regulamentações
A manutenção e verificação regular das válvulas de segurança também são essenciais para garantir a conformidade com normas e regulamentações aplicáveis. Muitas indústrias são obrigadas a seguir diretrizes rigorosas que exigem a manutenção regular de equipamentos de segurança.
As empresas devem estar cientes das normas específicas que se aplicam ao seu setor e garantir que suas práticas de manutenção estejam em conformidade. A não conformidade pode resultar em multas, processos legais e danos à reputação da empresa.
7. Conclusão
Em resumo, a manutenção e verificação regular das válvulas de segurança são práticas essenciais para garantir a segurança e a eficiência dos sistemas industriais. Investir em um programa de manutenção preventiva, treinar a equipe e monitorar continuamente o desempenho das válvulas são passos fundamentais para proteger tanto os trabalhadores quanto as instalações. Com a abordagem correta, as empresas podem operar com confiança, sabendo que suas válvulas de segurança estão prontas para agir quando necessário.
Em conclusão, a calibração de válvulas de segurança é uma prática indispensável para a operação segura e eficiente de sistemas industriais. Através da calibração adequada, é possível garantir que essas válvulas funcionem corretamente, protegendo equipamentos e prevenindo acidentes. Além disso, a manutenção regular e a verificação contínua são essenciais para assegurar que as válvulas permaneçam em condições ideais de operação. Ao seguir os passos corretos e evitar erros comuns, as empresas podem não apenas cumprir com as normas de segurança, mas também otimizar seus processos operacionais, resultando em um ambiente de trabalho mais seguro e produtivo.