Calibração de Válvulas de Segurança para Garantir a Segurança Industrial
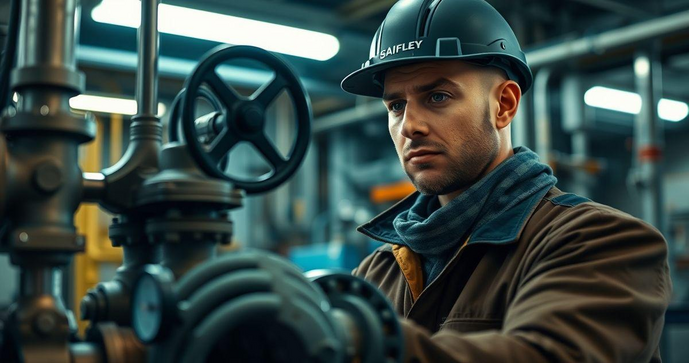
Por: Thiago - 17 de Abril de 2025
Importância da Calibração de Válvulas de Segurança
A calibração de válvulas de segurança é fundamental para garantir a integridade e a segurança de processos industriais. Essas válvulas desempenham um papel crucial ao liberar pressão excessiva, evitando explosões e danos a equipamentos e instalações. Portanto, a sua calibração correta é essencial para prevenir falhas catastróficas.
Um dos principais aspectos da importância da calibração é a conformidade com as normas de segurança. Muitas indústrias estão sujeitas a regulamentações rigorosas que exigem inspeções regulares e calibrações das válvulas de segurança. A não conformidade pode resultar em penalidades severas, incluindo multas e interrupções nas operações.
Além disso, válvulas de segurança bem calibradas aumentam a eficiência operacional. Quando esse tipo de equipamento funciona de maneira adequada, ele pode contribuir para a manutenção adequada da pressão em sistemas, levando a uma operação mais econômica e eficiente. Isso resulta em uma produção mais estável e um melhor gerenciamento de recursos.
Outro ponto a ser considerado é a proteção do patrimônio e da vida humana. Em setores como o químico, petroquímico e de geração de energia, o uso de válvulas de segurança mal calibradas pode colocar em risco empregados e instalações. A calibração regular é uma medida preventiva que ajuda a manter um ambiente de trabalho seguro e protegido.
Por fim, a manutenção e a calibração adequadas das válvulas de segurança podem reduzir os custos com reparos e manutenção de maquinário ao longo do tempo. Com a prevenção de falhas maiores, as indústrias podem economizar significativamente em custos de manutenção e evitar a necessidade de substituições dispendiosas.
Etapas do Processo de Calibração
O processo de calibração de válvulas de segurança deve seguir etapas metódicas para assegurar sua precisão e eficácia. Cada passo é essencial para garantir que a válvula funcione conforme as especificações do fabricante e os requisitos das normas de segurança.
1. Preparação: Antes de iniciar a calibração, é fundamental preparar o local de trabalho. Isso inclui a verificação de ferramentas e equipamentos necessários, como manômetros, chaves de fenda e válvulas de teste. Garanta que a área esteja limpa e que todos os materiais estejam à mão para evitar interrupções durante o processo.
2. Isolamento da Válvula: A válvula de segurança a ser calibrada deve ser isolada do sistema. Isso pode envolver o fechamento de válvulas adjacentes e a drenagem de pressão no sistema, garantindo um ambiente seguro para trabalhar. A segurança é a prioridade máxima neste passo.
3. Conexão de Equipamentos de Medição: Após isolar a válvula, conecte os dispositivos de medição, como manômetros ou transdutores, que serão utilizados para a calibração. Esses equipamentos devem ser calibrados e certificados, pois a precisão das medições é crucial para resultados confiáveis.
4. Teste Inicial: Realize um teste inicial da válvula. Isso envolve a aplicação gradual de pressão até alcançar o ponto de abertura da válvula. Durante esta etapa, observe o comportamento da válvula e registre a pressão na qual a válvula começa a abrir.
5. Ajustes Necessários: Com base nos resultados do teste inicial, faça os ajustes necessários. Isso pode incluir a modificação da pressão de abertura da válvula, se estiver fora das especificações. Alguns modelos possuem um mecanismo de ajuste que facilita essa modificação.
6. Testes de Verificação: Após realizar os ajustes, é importante realizar novos testes para verificar se a válvula está funcionando corretamente. Aplique pressão novamente e observe se ela opera nos limites adequados. Faça relatórios das medições obtidas durante esses testes.
7. Documentação: Finalmente, toda a calibração deve ser documentada. Isso inclui registros das medições antes e após os ajustes, os procedimentos realizados e qualquer recomendação para futuras calibrações. Essa documentação é crucial para auditorias e conformidade com normas regulatórias.
Seguir essas etapas meticulosas ajudará a garantir que as válvulas de segurança operem corretamente, contribuindo para a segurança e eficiência operacional das instalações industriais.
Equipamentos Necessários para Calibração
A calibração de válvulas de segurança requer o uso de equipamentos apropriados para garantir a precisão e a eficácia do processo. Investir nos dispositivos corretos não apenas facilita a calibração, mas também assegura que as medições sejam confiáveis e dentro das especificações requeridas.
A seguir, apresentamos os principais equipamentos necessários para a calibração de válvulas de segurança.
1. Manômetros: Os manômetros são essenciais para medir a pressão interna da válvula. Eles devem ser calibrados e ter a capacidade de medir a faixa de pressão que a válvula deve suportar. A precisão do manômetro impacta diretamente na exatidão dos resultados da calibração.
2. Testador de Válvulas: Este dispositivo é utilizado para simular diferentes condições de pressão e verificar o desempenho da válvula de segurança. Testadores podem incluir recursos avançados, como a capacidade de registrar dados automaticamente durante o processo de teste.
3. Chaves de Fenda e Ferramentas Manuais: Ferramentas manuais são necessárias para desmontar e ajustar as válvulas, conforme necessário. É importante ter chaves de fenda, alicates e outras ferramentas específicas para o modelo da válvula em calibração.
4. Equipamento de Segurança: Sempre que se trabalha com pressão, a segurança deve ser a prioridade. Equipamentos de proteção individual (EPIs), como luvas, óculos de segurança e protetores auditivos, devem ser utilizados para garantir a segurança do operador durante o processo de calibração.
5. Equipamentos de Registro: Manter registros precisos é essencial. Usar um tablet ou um computador portátil pode facilitar a documentação dos resultados da calibração, permitindo que os dados sejam salvos digitalmente e acessíveis para consultas futuras.
6. Software de Gestão: Em ambientes industriais que requerem calibrações frequentes, o uso de software de gestão de calibrações pode otimizar o processo. Esses softwares permitem agendar calibrações, rastrear resultados e garantir que toda a documentação necessária seja mantida organizada.
Ter os equipamentos corretos não só garante a precisão da calibração, mas também ajuda a melhorar a eficiência do processo. Ao utilizar esse conjunto de ferramentas, as indústrias podem assegurar que suas válvulas de segurança estejam sempre em conformidade com as normas de segurança e operando de forma eficaz.
Frequência Recomendada para Calibração
A frequência de calibração de válvulas de segurança é um fator crítico para garantir a segurança e a eficiência operacional em ambientes industriais. Determinar a periodicidade ideal para este procedimento depende de vários fatores, incluindo as especificações do fabricante, as normas regulatórias aplicáveis e as condições de operação da válvula. A seguir, discutiremos as recomendações gerais sobre a frequência de calibração.
1. Normas da Indústria: Muitas indústrias devem seguir normas específicas que estabelecem frequências mínimas para a calibração de válvulas de segurança. Por exemplo, setores como o químico e petroquímico estão sujeitos a regulamentações rigorosas que exigem calibrações anuais ou semestrais, conforme as diretrizes da OSHA ou da ANP.
2. Recomendação do Fabricante: Além das normas da indústria, é sempre importante consultar o manual do fabricante da válvula. Os fabricantes geralmente fornecem recomendações sobre a frequência de calibração, que são baseadas em testes e pesquisas. Seguir essas diretrizes ajuda a garantir que a válvula funcione como esperado.
3. Fatores de Uso: A frequência de calibração também pode ser influenciada pelos fatores de uso, como a pressão de operação e a frequência de ativação da válvula. Válvulas que operam sob altas pressões ou que são acionadas com frequência podem exigir calibrações mais regulares. Especialistas recomendam realizar uma calibração a cada 6 meses para estas válvulas.
4. Condições Ambientais: A presença de condições adversas, como corrosão, umidade ou temperaturas extremas, também pode impactar a necessidade de calibração. Em ambientes hostis, pode ser necessário realizar calibrações com mais frequência, podendo ser trimestral ou até mensal, dependendo do nível de agressividade do ambiente.
5. Histórico de Desempenho: Monitorar o desempenho anterior das válvulas pode ajudar a determinar a frequência ideal. Se problemas de desempenho forem identificados, a calibração deve ser realizada imediatamente e a frequência revisada. Documentar falhas ou irregularidades pode ajudar a prevenir futuros problemas de segurança.
Em resumo, estabelecer uma frequência de calibração adequada para válvulas de segurança é essencial para garantir a funcionalidade e a segurança em processos industriais. Seguir as recomendações do fabricante, considerar as normas da indústria e monitorar o desempenho histórico são passos fundamentais para determinar a periodicidade ideal. Desta forma, as empresas podem minimizar riscos e garantir a proteção de seus colaboradores e ativos.
Soluções para Problemas Comuns em Válvulas de Segurança
Válvulas de segurança são componentes críticos para a segurança de sistemas industriais, mas podem apresentar problemas ao longo do tempo. Identificar e resolver esses problemas comuns é essencial para garantir a eficácia e a segurança do equipamento. A seguir, abordaremos algumas soluções para questões frequentemente encontradas em válvulas de segurança.
1. Válvula Não Abrindo: Um dos problemas mais comuns é a válvula não abrir quando a pressão ultrapassa o limite estipulado. Isso pode ser causado por resíduos ou sujeira acumulada na válvula. A solução inclui a desmontagem da válvula e a limpeza cuidadosa de todos os componentes. Além disso, certifique-se de que a válvula não esteja presa devido a corrosão ou desgaste mecânico.
2. Válvula Abrindo Prematuramente: Se a válvula abre antes da pressão desejada, isso pode indicar um problema de ajuste. Neste caso, é necessário recalibrar a válvula para garantir que a pressão de abertura esteja de acordo com as especificações do fabricante. Consultar o manual e ajustar a pressão de abertura pode resolver o problema.
3. Vazamentos: Vazamentos são outro problema sério que pode ocorrer em válvulas de segurança. Se houver presença de fluídos ao redor da válvula, é imperativo verificar as juntas e selos, pois podem estar deteriorados. Substituir essas peças pode resolver o problema de vazamento e garantir a integridade do sistema.
4. Barulhos Estrondosos: Barulhos incomuns durante a operação, como rangidos ou estalos, podem indicar que as partes internas da válvula estão desgastadas ou mal lubrificadas. Neste caso, a válvula deve ser inspecionada para identificar partes danificadas e, se necessário, aplicar lubrificantes adequados ou substituir as peças danificadas.
5. Inatividade Prolongada: Válvulas que não são utilizadas frequentemente podem apresentar problemas quando finalmente acionadas. Para evitar isso, recomenda-se a realização de testes periódicos, mesmo em válvulas que não são acionadas regularmente. Realizar uma manutenção preventiva para manter as válvulas em funcionamento ajudará a evitar falhas futuras.
6. Falhas Eletrônicas: Válvulas de segurança que operam com sistemas eletrônicos podem apresentar falhas devido a problemas de fiação ou interferências. Para resolver isso, é necessário inspecionar as conexões elétricas e verificar o funcionamento de sistemas de controle. Caso haja falhas persistentes, um eletricista qualificado deve ser chamado para realizar os reparos necessários.
Ao abordar essas questões comuns em válvulas de segurança, as indústrias podem evitar problemas sérios que possam comprometer a segurança e a operação eficiente de seus sistemas. A manutenção regular e a detecção precoce de falhas são fundamentais para a eficácia a longo prazo das válvulas de segurança.
Benefícios a Longo Prazo da Calibração Adequada
A calibração adequada de válvulas de segurança traz uma série de benefícios a longo prazo que são fundamentais para a operação eficiente e segura de instalações industriais. Esses benefícios não apenas garantem a conformidade com as normas regulatórias, mas também melhoram a confiabilidade e a durabilidade do equipamento. A seguir, abordaremos alguns dos principais benefícios a longo prazo da calibração apropriada.
1. Segurança Aprimorada: A calibração regular assegura que as válvulas de segurança funcionem corretamente dentro dos limites designados, minimizando assim o risco de falhas catastróficas. Com válvulas devidamente calibradas, a probabilidade de acidentes relacionados à pressão excessiva é reduzida, protegendo tanto os colaboradores quanto as instalações.
2. Maior Vida Útil do Equipamento: Investir em calibração regular contribui para a longevidade das válvulas de segurança. Quando calibradas adequadamente, essas válvulas sofrem menos desgaste e, consequentemente, apresentam uma vida útil mais prolongada. Isso reduz a necessidade de substituições frequentes e custos associados a novos equipamentos.
3. Eficiência Operacional: Equipamentos devidamente calibrados operam de maneira mais eficiente, resultando em melhor desempenho do sistema. Isso leva a uma redução no consumo de energia e nos custos operacionais, uma vez que os processos industriais podem funcionar de forma otimizada. A eficiência aprimorada também pode resultar em maior produtividade.
4. Redução de Custos com Manutenção: A calibração apropriada pode ajudar a evitar falhas e quebras dispendiosas. Isso se traduz em menores custos com manutenção, já que a detecção precoce de problemas permite que soluções sejam implementadas antes que uma falha ocorra. Dessa forma, as empresas podem evitar paradas inesperadas e seus custos associados.
5. Conformidade Regulatória: A calibração regular das válvulas de segurança ajuda as empresas a manterem-se em conformidade com as leis e regulamentações pertinentes. Isso não apenas protege a empresa contra penalidades, mas também fortalece sua reputação no mercado, demonstrando compromisso com a segurança e responsabilidade ambiental.
6. Melhoria na Imagem Empresarial: Empresas que priorizam a calibração e a manutenção de seus equipamentos são vistas como mais responsáveis pelos clientes e pela comunidade. Isso pode aumentar a confiança e a lealdade à marca, além de atrair novos clientes que valorizam práticas de segurança robustas.
Considerando esses benefícios, fica evidente que a calibração adequada de válvulas de segurança não é apenas uma questão de conformidade, mas uma estratégia essencial para a segurança, eficiência e rentabilidade a longo prazo de operações industriais. Implementar um programa de calibração eficaz é, portanto, uma prática recomendada para garantir uma operação otimizada e segura.
A calibração de válvulas de segurança é uma prática indispensável para ambientes industriais que buscam assegurar a segurança, eficiência e conformidade operacional.
Através de um processo metódico que inclui a preparação, testes, ajustes e documentação, as empresas podem aferir que suas válvulas funcionem de acordo com as especificações necessárias, prevenindo acidentes e falhas dispendiosas.
Além disso, a escolha dos equipamentos adequados e a consideração para a frequência de calibração são essenciais para maximizar a eficácia do equipamento.
Os benefícios a longo prazo, como a segurança superior, a maior vida útil do equipamento e a eficiência operacional, são fundamentais para solidificar um ambiente de trabalho seguro e produtivo.
Priorizar a calibração não apenas protege investimentos, mas também reforça a confiabilidade e a imagem institucional da empresa no mercado.
Portanto, implementar um programa robusto de calibração de válvulas de segurança deve ser uma prioridade para todos os setores que operam com sistemas pressurizados.